We sat down with Professor Kathrin Dörfler of the Technical University of Munich (TUM) in advance of WDBE 2020. We discussed the importance of innovation and how her research focuses on the need for practical and productive solutions when it comes to on-site support.
Digital and technical innovation plays an essential role in optimizing the modern built environment. Now leading the Augmented Fabrication Lab (AFAB) in TUM, Professor Kathrin Dörfler quickly saw the need for practical solutions early in her career.
The Importance of ‘Need’
“I’m originally an architect,” she says. “I studied digital art and architecture and my tendency to go toward digital fabrication came from this proximity to computational design and the need to use robots for fabrication. There was no other way to build the things you created in your virtual space without using machinery.”
This ‘need’ characterizes many of the issues facing the sector, with the last ten years seeing an explosion of interest in digital innovation. This was also accompanied by an increased capacity to build the tools that were needed, but often saw the creation of projects that were cutting edge…but impractical.
But the need for practical change was always at the front of researchers’ minds.
“They didn’t stay within the realm of prototypes,” says Prof. Dörfler. “But they went into real scale-building scenarios. Working closely with the industry to show what is actually possible and make it real.”
Tackling Real-World Problems
This focus on the practical comes alongside the development of a challenging work environment. One that is defined by the threat of climate change, a need for green builds, calls for closed-loop manufacturing, and support for the most precious resource of all – optimized labor.
This led Prof. Dörfler and her team to focus on Mobile Additive Manufacturing through a research project that aims to help armature-equipped robots operate in scenarios where the scale and nature of the build exceeds the capacity of a static or conventional unit. This allows them to be used offsite in pre-builds or to be taken on location. Using a rig of sensors and controls, the unit provides contextual awareness and the ability to adapt to the real-world requirements of daily use. This ranges from changes in terrain and environment, to a position in a busy construction chain.
Tackling this challenge required novel sensing strategies and a capacity for adaptive behavior, all with an eye for full autonomy; aiming to help to solve problems from an architectural and engineering position.
Helping Humans Work
But despite this focus on technology, the creation of new kit is not a goal in itself.
“I would say the main focus I’d be interested in right now is bringing the human back into the picture,” says Prof. Dörfler.
She adds that while technology is increasing at a faster rate, the need to work in collaboration helps optimize the approach for both.
“The construction sector is very dispersed and what we are dealing with is a number of decentralized systems,” she continues. “Construction companies are not one huge entity that can implement a huge change in workflow. So, when we think of human/robot collaborative scenarios, we also think of attaching or integrating technology locally.”
This ideal of localized attachment is important to Prof. Dörfler and her work, as “it seems that we can make much more of an impact if we introduce technology in parts – this means something that doesn’t replace the established workflow as we know it.”
Contextualized Automation Today
Having an awareness of the social-cultural context of adding new tools becomes vital, as does taking a modular approach to implementation. Instead of operating in the abstract, the question of ‘what brings more benefit to day-to-day work’ leads her team’s research. Or, as she puts it: “we’re learning that it’s not efficient and productive to automate from A to Z. But to automate from E to F – just one segment of the chain – that really makes the most sense”.
It was this technology that led to one of her other innovations – Augmented Brickwork – a collaboration with Gramazio Kohler Research and the start-up incon.ai. This resulted from the removal of the sensor system from their Mobile Additive Robot and combining it with a visual interface to help deliver precise geometric information to on-site workers. For their team, this bridged the gap in operational capacity between the problem-solving capacity of a human and the accuracy of a machine.
“We instruct bricklayers through this augmented reality or mixed reality interface to build very precise geometric building components according to the 3-D model,” explains Prof. Dörfler. “It gave us a platform to open a completely new side of this whole context of digital fabrication – where you don’t only look into automating everything.”
Prioritizing Selective Support
She leads her team at TUM to prioritize and fulfill validated need over simple demonstrations of what is ‘possible’ with their equipment – moving from ‘we built what we can’ to ‘we build what we actually require’.
“We have to develop and create these complementary systems,” adds Prof. Dörfler. “One of the things that is always in the back of our minds is moving away from digital fabrication representing only crazy forms and shapes and to create integrated, smart, and sustainable processes instead.”
This continued focus on practicality over the explicitly academic is something that Prof. Dörfler is keen to embed throughout her work.
“I’m trying to build up my lab in the most interdisciplinary manner that I can,” she says. “To not have a major division between academia and industry, but to work closely on projects so that the know-how and the knowledge transfer happens intrinsically. I think that can only happen with industry collaborative projects.”
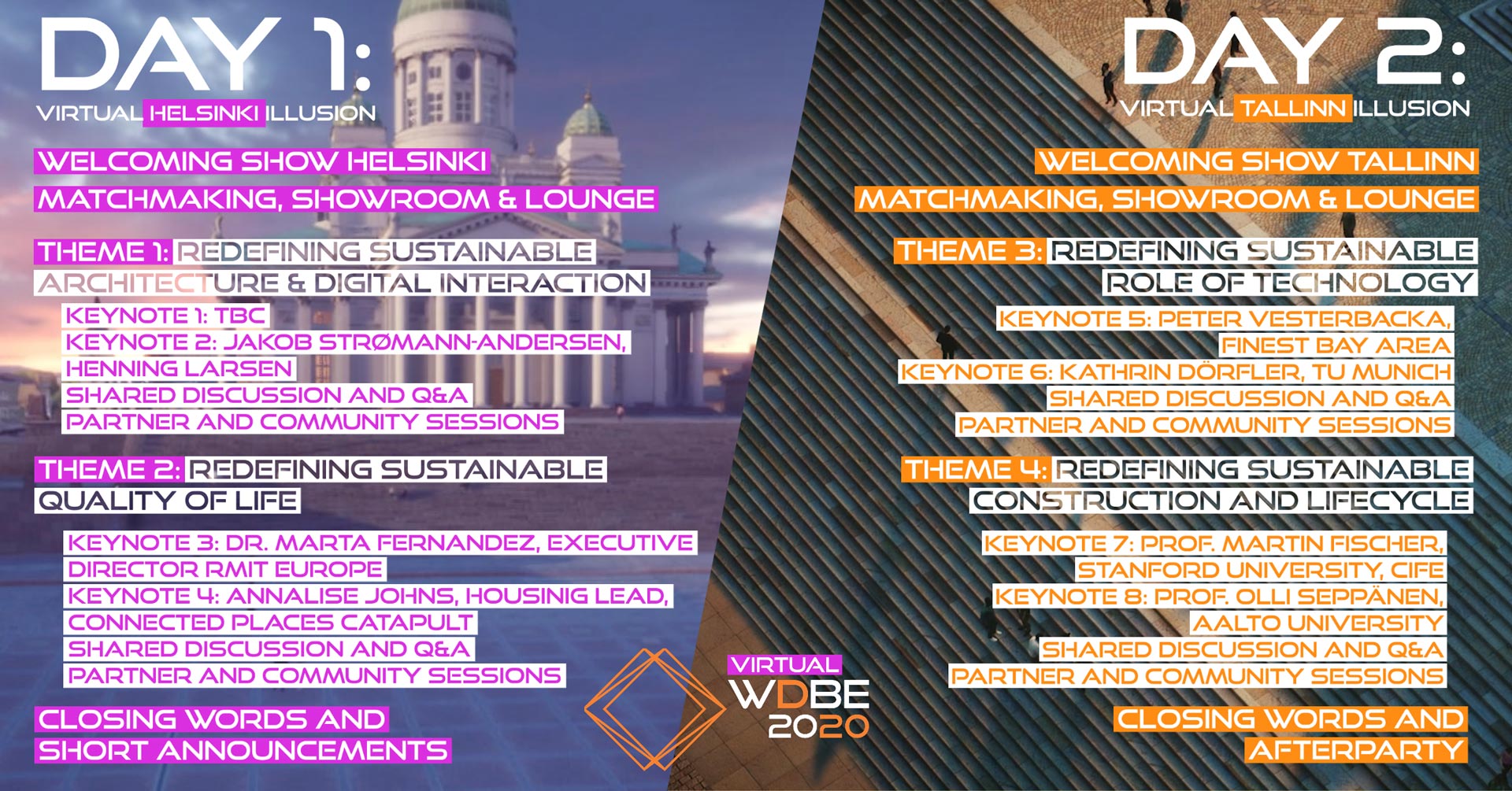
What’s Next?
Speaking about WDBE, Prof. Dörfler will be covering these themes and more.
“I’ll be continuing the conversation about human/robot collaborative processes,” she says. “Basically, what is the role of the human in our age of automation and the role of robotics in on-site construction and digital fabrication.”
While there may still be a way to go for the sector and there will surely be many challenges ahead, she is optimistic about the future.
“As far as I’ve personally experienced it, interest from the industry grows rapidly,” she says. “And it grows by having prototypes – building one-to-one scale so that they can see the benefit in the real world… and that it actually works (laughs). It’s something we’re building up to now, so I’m very excited about the potential applications ahead of us.”
Professor Kathrin Dörfler will be speaking at WDBE on 29th-30th September 2020. You can book tickets here or learn more about the other events and learn more about the regularly updated agenda from here.
This article originally appeared at WDBE.org.
Responses